Most current works in Sim2Real learning for robotic manipulation tasks leverage camera vision that may be significantly occluded by robot hands during the manipulation. Tactile sensing offers complementary information to vision and can compensate for the information loss caused by the occlusion. However, the use of tactile sensing is restricted in the Sim2Real research due to no simulated tactile sensors being available. To mitigate the gap, we introduce a novel approach for simulating a GelSight tactile sensor in the commonly used Gazebo simulator. Similar to the real GelSight sensor, the simulated sensor can produce high-resolution images by an optical sensor from the interaction between the touched object and an opaque soft membrane. It can indirectly sense forces, geometry, texture and other properties of the object and enables Sim2Real learning with tactile sensing. Preliminary experimental results have shown that the simulated sensor could generate realistic outputs similar to the ones captured by a real GelSight sensor.
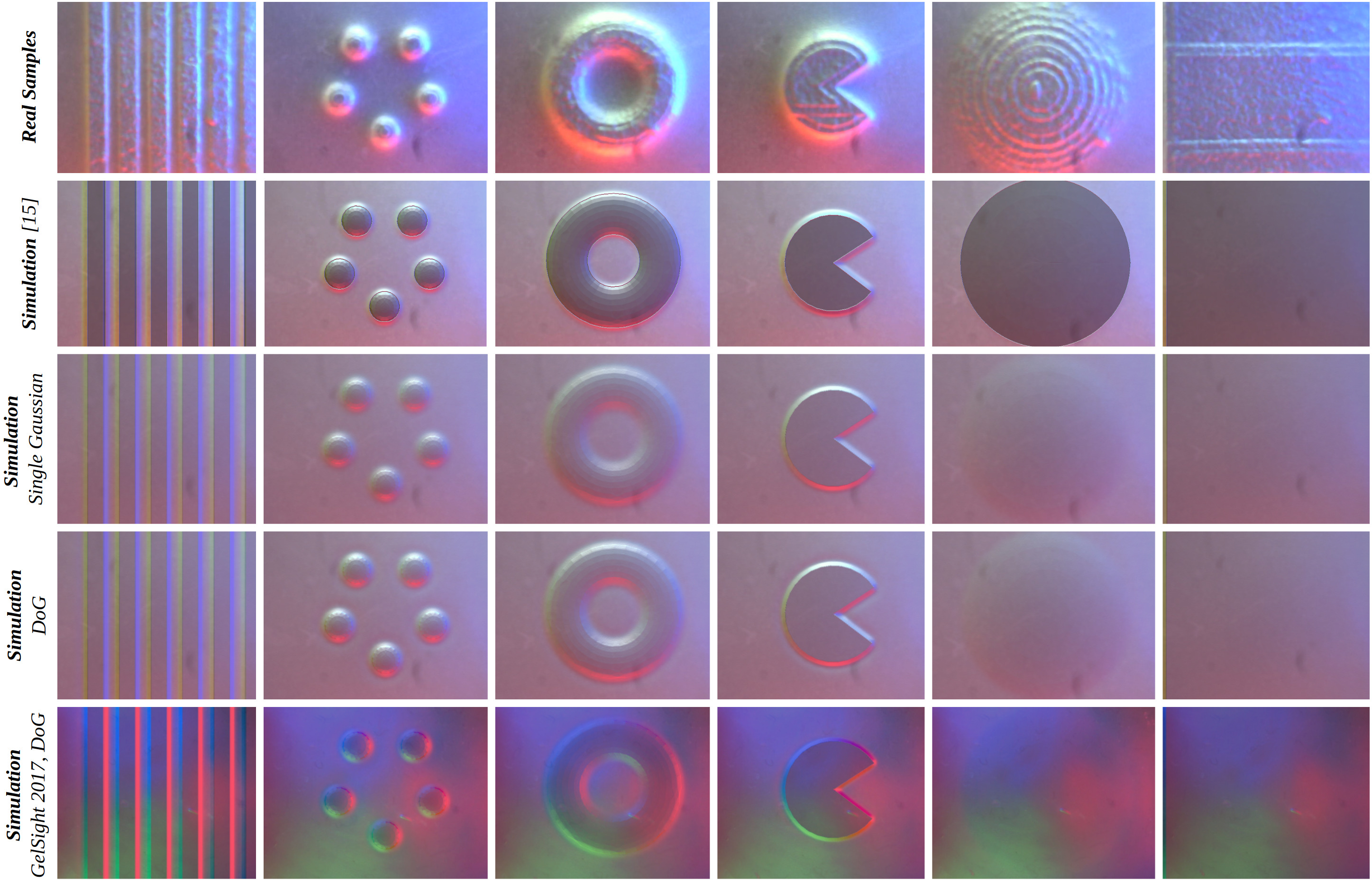
ViTac workshop
This GelSight Simulation method was firstly proposed at the 2019 ICRA ViTac Worshop and, given the interest shown by the community, now revised and extended in a new publication[1]. For instance, the initial elastomer deformation approximation approach, generated unrealistic sharp contouring around the in-contact areas, as shown in Figure 2. Improvements achieved now, are shown in Figure 3.
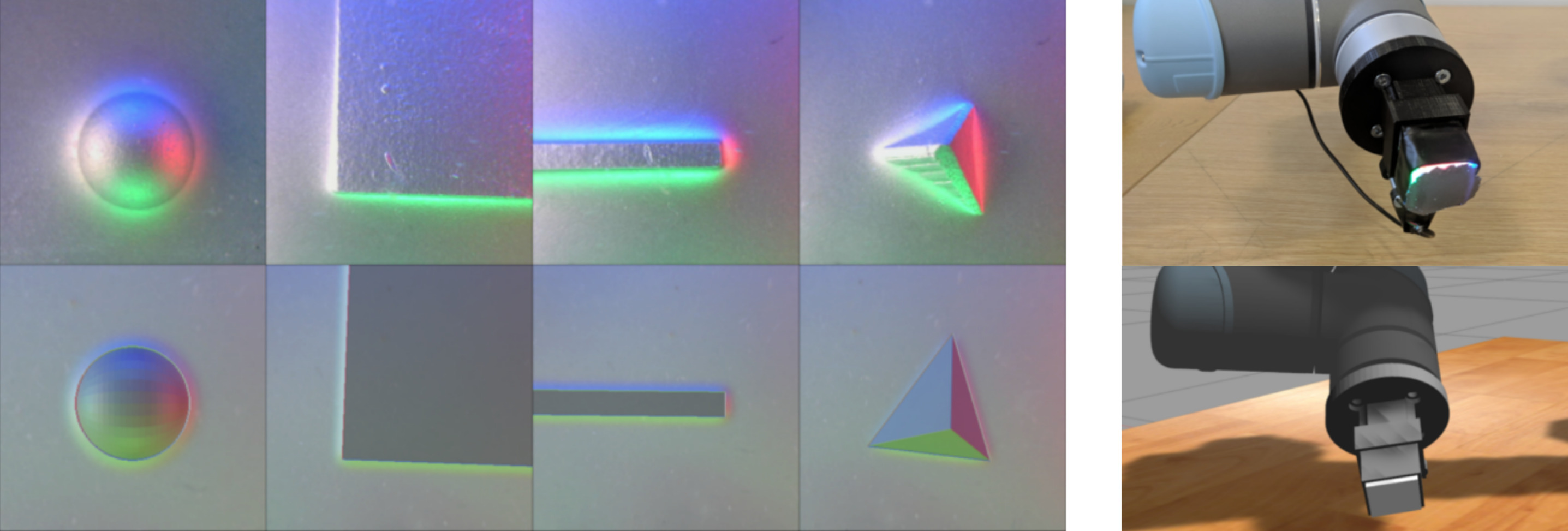
Method

Experimental Setup
To produce the necessary real datasets, a GelSight sensor is mounted onto a Fused Deposition Modeling (FDM) 3D printer A30 from Geeetech. A set of objects with different shapes on the top is designed and 3D printed using the Form 2 Stereolithography (SLA) 3D printer. A Virtual World comprised of a FDM printer, a GelSight sensor and a set of virtual objects, is also set up. Identical real and virtual datasets are then collected.
These include the STL files for printing the 21 set of objects and support mount,
the raw real and virtual datasets, and the aligned datasets using the per-object alignment method.
Please refer to the paper for more details about the experiments.

Sim2Real transfer learning
One aspect to consider in the Sim2Real learning is the Sim2Real gap that results from characteristics of the real world being not modeled in the simulation. In our case, we find that one major difference between the real and synthetic samples are the textures introduced by the 3D printing process. To mitigate this issue, we create twelve texture maps using GIMP that resemble the textures observed in the real samples, as shown in Figure 1. By randomly perturbing the captured virtual depth-maps with such textures, we are able to produce an effective data augmentation scheme that significantly improves the Sim2Real transition, from a 43.76% classification accuracy to 76.19%, in the real data.
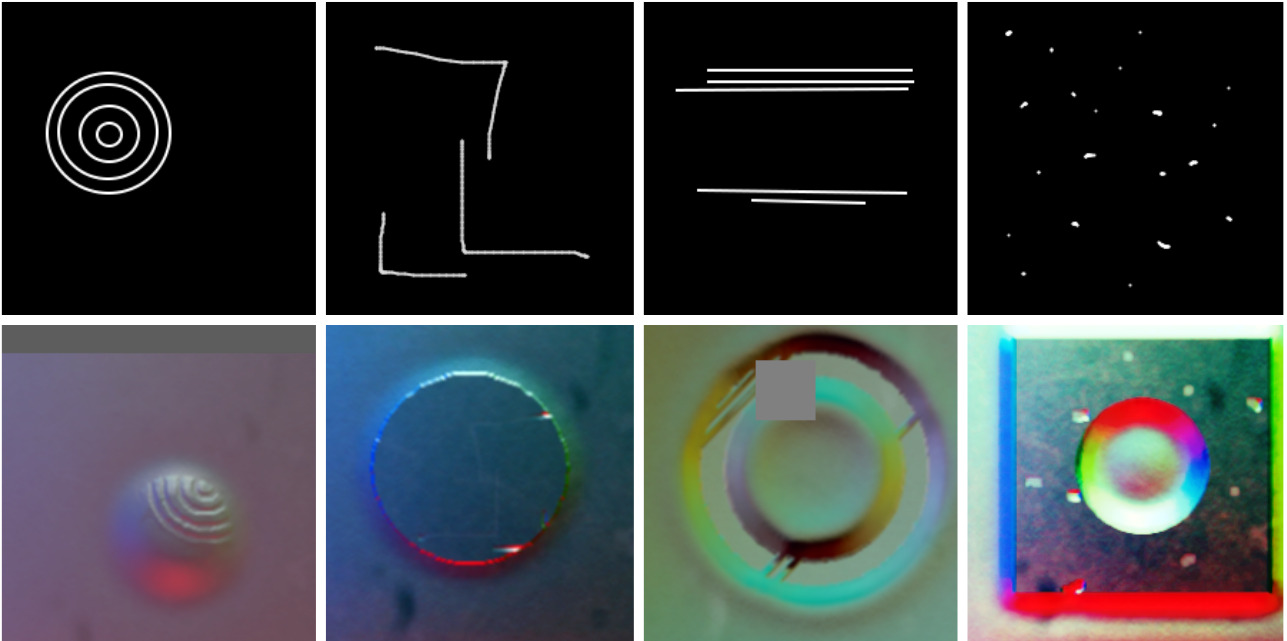
References
- 1.Daniel Fernandes Gomes, Paolo Paoletti and Shan Luo, "Generation of GelSight Tactile Images for Sim2Real Learning", RA Letters, ArXiv preprint ↩
- 2.Daniel Fernandes Gomes, Achu Wilson and Shan Luo, "GelSight Simulation for Sim2Real Learning", ViTac Workshop ICRA 2019. paper ↩